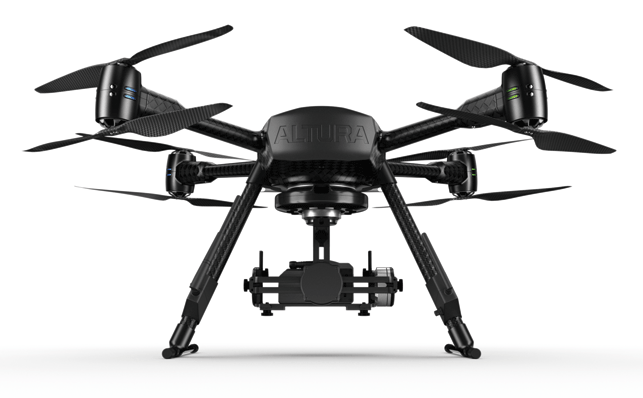
Aerialtronics utvikler kundetilpassede droner og bruker Stratasys 3D-printer for raskt og kostnadseffektivt kunne produsere sterke og lette deler i ABS. Dette gjør at de kan fullføre mange iterasjoner uten skyhøye kostnader.
Tilpassede droner for ulike kundebehov
Aerialtronics har utviklet et standardprodukt som kan tilpasses individuelle kunder og bruksområder.
Resultatet av vårt utviklingsarbeid er Altura Zenith. De spesialtilpassede delene inkluderer motorkraft, nyttelastkapasitet, flytid og nødvendig programvare.
— Joost Hezemans, sjefskonstruktør i Aerialtronics.
Standarddelene består av motorrom, ulike balanseringer samt bokser og rom for maskin- og programvare – som alle krever konstruksjon og prototyper.
Utviklingsprosessen trengte en raskere løsning
Tidligere outsourcet Aerialtronics prototypeproduksjonen, noe som førte til lange ledetider og høye kostnader, spesielt når prototyper ble produsert i Asia med måneders ventetid. For å få fart på prosessen, bygde de opp en egen 3D-utskriftsavdeling ved hjelp av Stratasys uPrint SE Plus.
Aerialtronics hadde som mål å begrense utviklingstiden og kostnadene, og lette derfor etter en raskere og mer kostnadseffektiv løsning. I tett samarbeid med Stratasys bygde selskapet til slutt en egen 3D-utskriftsvirksomhet basert på Stratasys uPrint SE Plus 3D-printer.
ABSplus har perfekte vektegenskaper
Siden Aerialtronics tok kontroll over prototypemodellproduksjonen selv, har de redusert de lange ledetidene de tidligere hadde. Tidsprosessen for FoU er redusert med cirka 50 prosent.
Vi liker enkelheten i hvordan våre CAD-design kan mates direkte inn i en Stratasys 3D-printer. ABSplus har den riktige styrken og de ideelle vektegenskapene som kreves for å bygge en komplett flygende prototype. En ekstra fordel med ABSplus er at den kan brukes i vår produksjon av standarddeler.
— Joost Hezemans, sjefskonstruktør i Aerialtronics.
Motorene kan generere mye varme, så det er veldig viktig å ha et materiale som tåler dette samtidig som det har riktig styrke og vekt. De 3D-printede ABSplus-motorfestene har disse egenskapene.
Raskere iterasjoner og forbedrede sluttprodukter
Dronenes hovedplattformer produseres i karbonfiber, men 3D-printeren brukes til deler som sensorer, videolinker og GPS-kapsler, noe som ytterligere effektiviserer prosessen. Teknologien gir teamet mulighet til å justere designet og teste nye deler daglig, noe som resulterer i flere iterasjoner og et sluttprodukt av høyere kvalitet.
Noen typiske eksempler er 3D-printede deler som skal romme sensorutstyr, videokoblingsutstyr og GPS-systemer i ulike størrelser og bokser for kabler og elektroniske komponenter. Bruken av 3D-printere har også gitt designere og ingeniører mer tid til å foredle komponenter.
Med uPrint 3D-printer kan vi justere konstruksjonen i løpet av dagen og printe ut nye deler i 3D i løpet av natten, teste, justere litt og printe ut en ny som vi kan teste dagen etter. Denne prosessen innebærer at designet har gjennomgått mellom fem og ti flere iterasjoner enn tidligere. Vi har vært i stand til å 3D-printe mer, se mer og fly mer enn det som var mulig tidligere. Takket være 3D-printeren blir sluttproduktet mye bedre.
— Joost Hezemans, sjefskonstruktør i Aerialtronics.